The Importance of Proper Material Handling for Warehouses
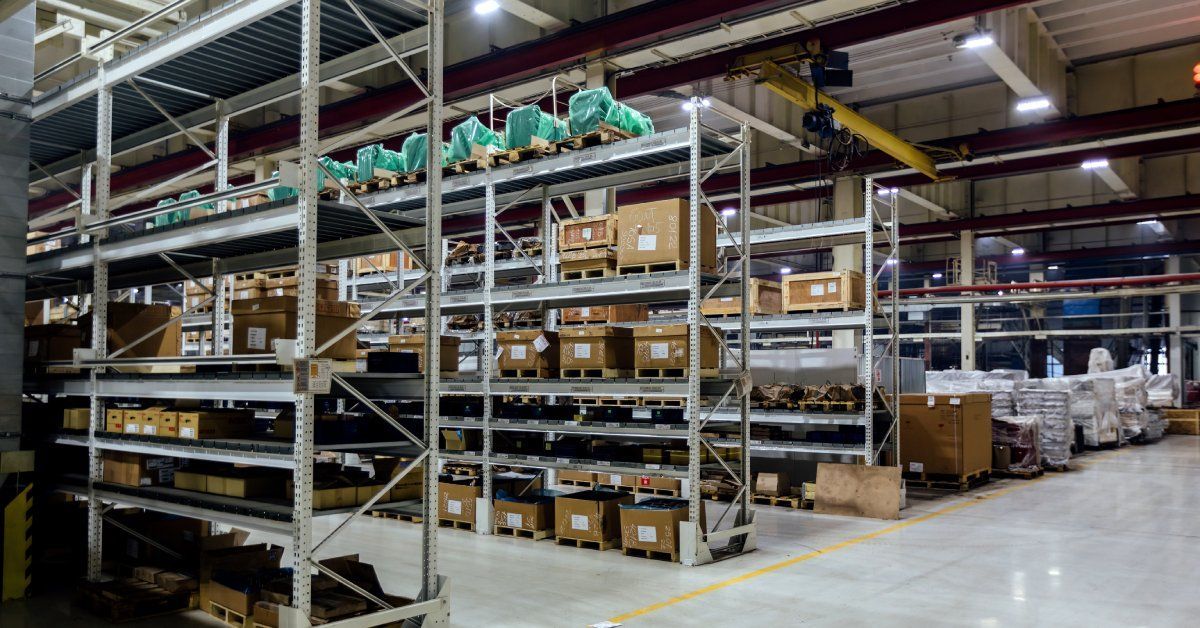
When it comes to warehousing, efficient material handling is the backbone of your operations. Properly managing the movement, storage, and control of goods can significantly impact your productivity, safety, and bottom line. Here, we’ll explore the importance of proper material handling for warehouses and share actionable insights to optimize your processes.
Why Material Handling Matters
Effective material handling is about more than just storing products and moving them from point A to point B. It’s a pivotal element that affects every aspect of your warehouse operations. By mastering material handling, you can boost efficiency, reduce costs, and enhance worker safety. Our guide will help you understand the essentials of proper material handling and how to apply them in your warehouse.
The Foundation of Efficient Warehousing
Streamlining Operations for Enhanced Productivity
Efficiency in material handling begins with streamlined operations. When you move and store goods efficiently, you minimize delays and boost overall productivity. Implementing standardized procedures ensures that every team member knows their role, reducing errors and improving workflow.
Reducing Operational Costs
Proper material handling can lead to significant cost savings. By minimizing the time and effort required to move products, you can reduce labor costs. Additionally, efficient handling reduces the risk of product damage, saving you money on replacements and repairs.
Ensuring Worker Safety
Safety is paramount in any warehouse. Proper material handling practices reduce the likelihood of accidents and injuries. By implementing ergonomic solutions and providing adequate training, you can create a safer work environment for your employees, which can also reduce liability and insurance costs.
Key Principles of Material Handling
Planning and Standardization
Planning is the first step toward effective material handling. Develop a comprehensive plan that outlines the movement of goods within the warehouse. Standardizing these processes ensures consistency, reduces confusion, and improves efficiency.
Ergonomics and Safety
Ergonomic solutions are essential for reducing worker fatigue and preventing injuries. Use equipment designed to minimize physical strain and ensure that workers receive training on proper lifting techniques as well as safe handling and storage practices.
Technology and Automation
Incorporating technology and automation can significantly benefit material handling efficiency. Automated systems, such as conveyor belts and robotic pickers, streamline the movement of goods, reduce human error, and free up workers for more complex tasks.
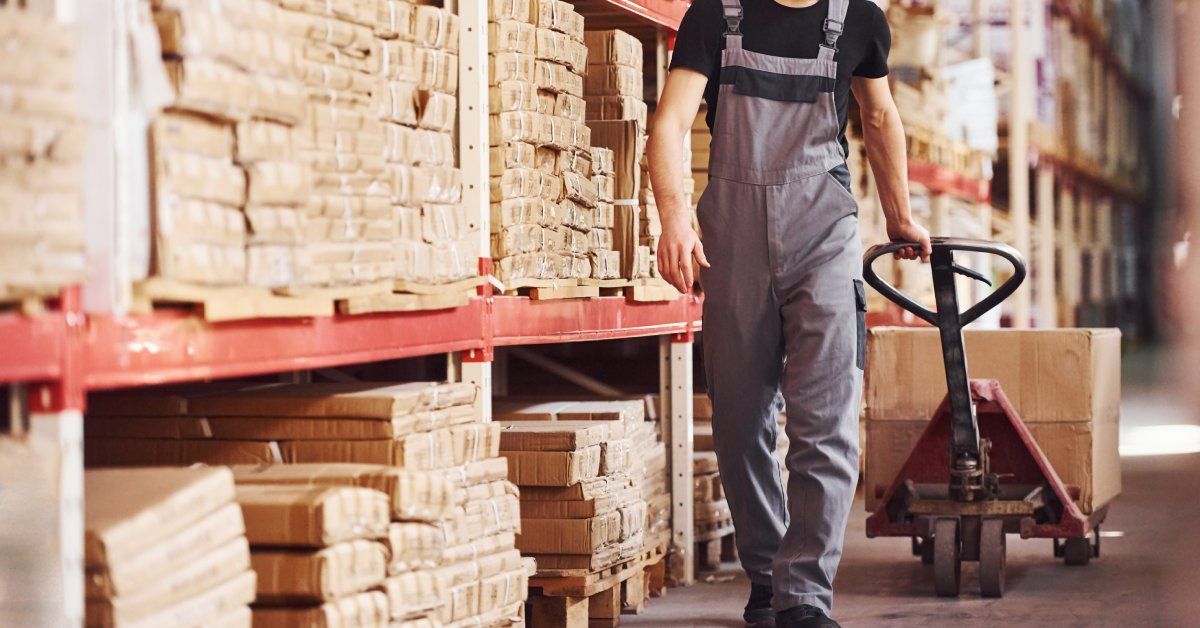
Optimizing Your Warehouse Layout
Strategic Placement of Goods
The placement of goods within your warehouse plays a crucial role in material handling efficiency. Store frequently picked items in easily accessible locations to minimize travel time and effort. Use data analytics to determine the optimal placement of products based on picking patterns and order frequency.
Vertical Space Usage
Maximize your storage capacity by utilizing vertical space. Implementing high-rise shelving, racking systems, and raised mezzanines allows you to store more goods without expanding your warehouse footprint. Ensure that you have the necessary equipment, such as forklifts and reach trucks, to safely access high shelves.
Clear Aisle Design
Designing clear and wide aisles is essential for smooth material handling. Narrow or cluttered aisles can slow down operations and increase the risk of accidents. Maintain clear pathways and implement signage to guide workers and equipment safely through the warehouse.
Implementing Efficient Picking Strategies
Batch Picking
Batch picking involves collecting multiple orders simultaneously, which reduces travel time and increases picking efficiency. Group orders with similar items together and use picking lists or automated picking systems to streamline the process.
Zone Picking
In zone picking, the warehouse is divided into different zones, with each worker responsible for picking items within their designated area. This method reduces worker movement and allows for faster order fulfillment. Implementing a conveyor system can further enhance picking efficiency.
Wave Picking
Wave picking is a hybrid approach that combines elements of batch and zone picking. The process groups orders into waves based on specific criteria, such as shipping deadlines or product types. Workers pick items for multiple orders within their zone, and the picked goods are then consolidated for final packing and shipping.
Training and Empowering Your Workforce
Implementing Comprehensive Training Programs
Proper training is essential for effective material handling. Develop comprehensive training programs that cover safe handling practices, equipment operation, and emergency procedures. Regularly update training materials to reflect new technologies and industry best practices.
Encouraging Continuous Improvement
Foster a culture of continuous improvement by encouraging workers to identify and report inefficiencies. Implement a feedback system where employees can suggest improvements and recognize those who contribute valuable ideas. Continuously assess and refine your material handling processes to stay ahead of industry trends.
Providing the Right Tools and Equipment
Equip your workforce with the tools and equipment they need to perform their tasks efficiently and safely. Invest in high-quality material handling equipment, such as pallet jacks, forklifts, and conveyor systems. Regularly maintain and inspect equipment to ensure it remains in optimal working condition.
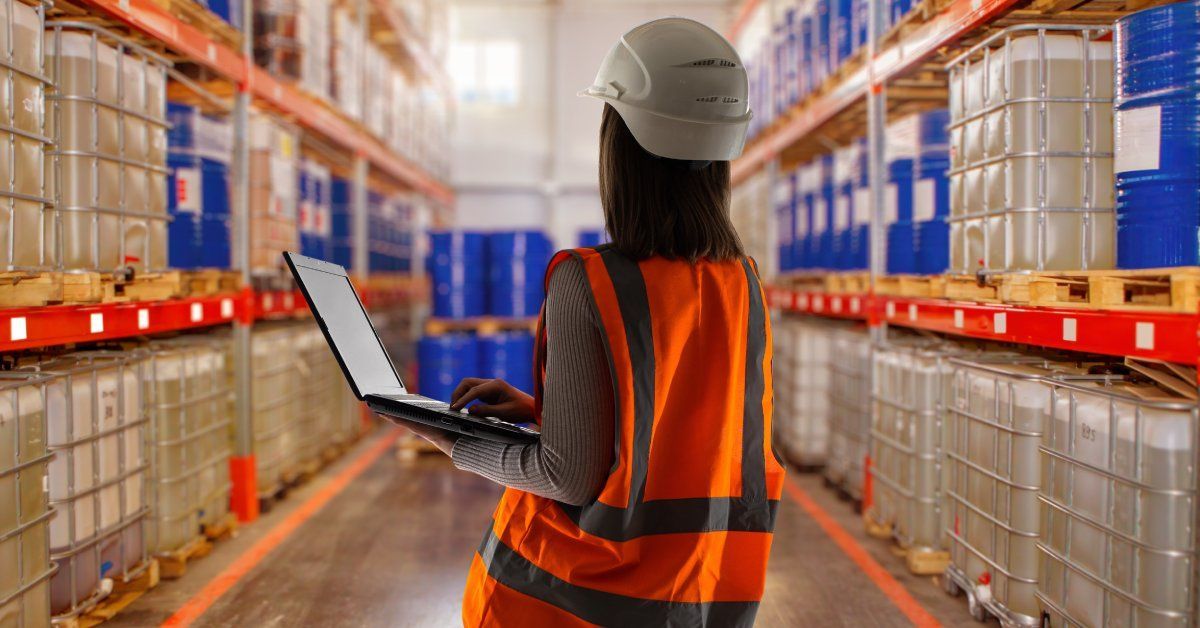
Leveraging Data and Analytics
Key Performance Indicators
Use data analytics to track key performance indicators (KPIs) related to material handling, such as order fulfillment time, picking accuracy, and equipment utilization. Analyzing these metrics can help you identify areas for improvement and measure the effectiveness of implemented changes.
Predictive Analytics
Predictive analytics can help you anticipate future trends and demands. By analyzing historical data, you can forecast inventory needs, optimize stock levels, and plan for peak periods. Implementing predictive analytics enables you to make data-driven decisions that enhance material handling efficiency.
Real-Time Monitoring
Real-time monitoring systems provide immediate insights into your material handling processes. Use sensors and tracking devices to monitor the movement of goods and equipment within the warehouse. Real-time data allows you to quickly address issues and make adjustments to improve efficiency.
Staying Ahead With Industry Trends
Adopting New Technologies
Stay ahead of industry trends by adopting new technologies that enhance material handling efficiency. Explore advancements in automation, robotics, and artificial intelligence to find innovative solutions that meet your warehouse needs.
Prioritizing Continuous Learning
Encourage continuous learning and development within your organization. Stay informed about industry trends and best practices through conferences, webinars, and industry publications. Investing in ongoing education ensures your team remains knowledgeable and able to adapt to changing demands.
Partnering With Experts
Partner with industry experts and consultants to gain insights and guidance on optimizing your material handling processes. Expert advice from Tyler Supply Company can help you identify innovative solutions and implement best practices that drive efficiency and growth.
Understanding the importance of material handling is essential for the success of any warehouse operation. By implementing the principles and strategies outlined in this guide, you can enhance efficiency, reduce costs, and ensure the safety of your workforce. Remember, continuous improvement and staying informed about industry trends are key to maintaining a competitive edge.
For material handling and storage in Michigan, no one has you covered like Tyler Supply Company. We have the expertise to make sure your warehouses run smoothly and efficiently for years to come.