How Rack Inspections Help Identify and Mitigate Risks
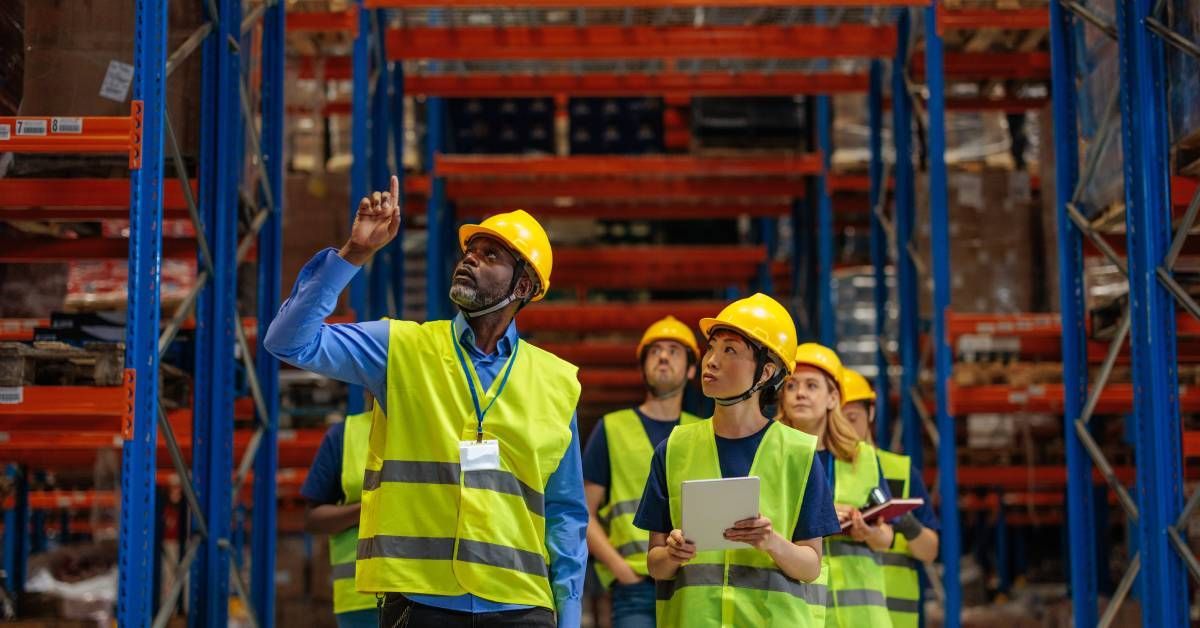
Running a warehouse is no small task. From managing inventory to coordinating staff, the demands on your time and attention can be overwhelming. But one responsibility stands above the rest: the safety and efficiency of your operation.
A single oversight in your storage systems can lead to costly downtime, product damage, or even employee injuries. Maintaining a safe, organized environment isn’t just about compliance for warehouse managers and operators; it’s about protecting your investment, your team, and your bottom line.
One often-overlooked yet critical factor in warehouse safety is the condition of your storage racks. These structures bear the weight of your inventory day in and day out, making them a vital part of your operation’s backbone. Rack inspections, when done regularly, provide a proactive way to identify structural issues, mitigate hazards, and prevent minor concerns from becoming major problems.
By incorporating routine inspections into your maintenance plan, you can enhance safety and improve operational effectiveness, setting up your warehouse for long-term success.
What Are Rack Inspections?
Before we dive into how rack inspections help identify and mitigate risks, it’s important to understand what they entail. Rack inspections are systematic evaluations of the storage racks used in warehouses to ensure they’re safe, stable, and functioning correctly. These inspections look for signs of damage, wear, or misalignment that could compromise the structural integrity of the racks.
Given that these racks often bear thousands of pounds of inventory, even a minor issue can lead to major consequences if left undetected. Rack inspections are essential for maintaining a safe work environment and complying with safety regulations and industry standards.
There are two primary types of rack inspections commonly used in warehouses: visual inspections and detailed inspections. Visual inspections are typically conducted by in-house staff on a regular basis to quickly spot obvious signs of damage, like bent beams or missing safety clips.
Detailed inspections, on the other hand, go a step further and are usually performed by trained professionals. These inspections involve a thorough examination of the racks, focusing on load capacities, material defects, and overall installation quality. Both types of inspections play a vital role in warehouse management, with visual checks offering day-to-day oversight and detailed inspections providing the in-depth analysis needed to prevent long-term issues.
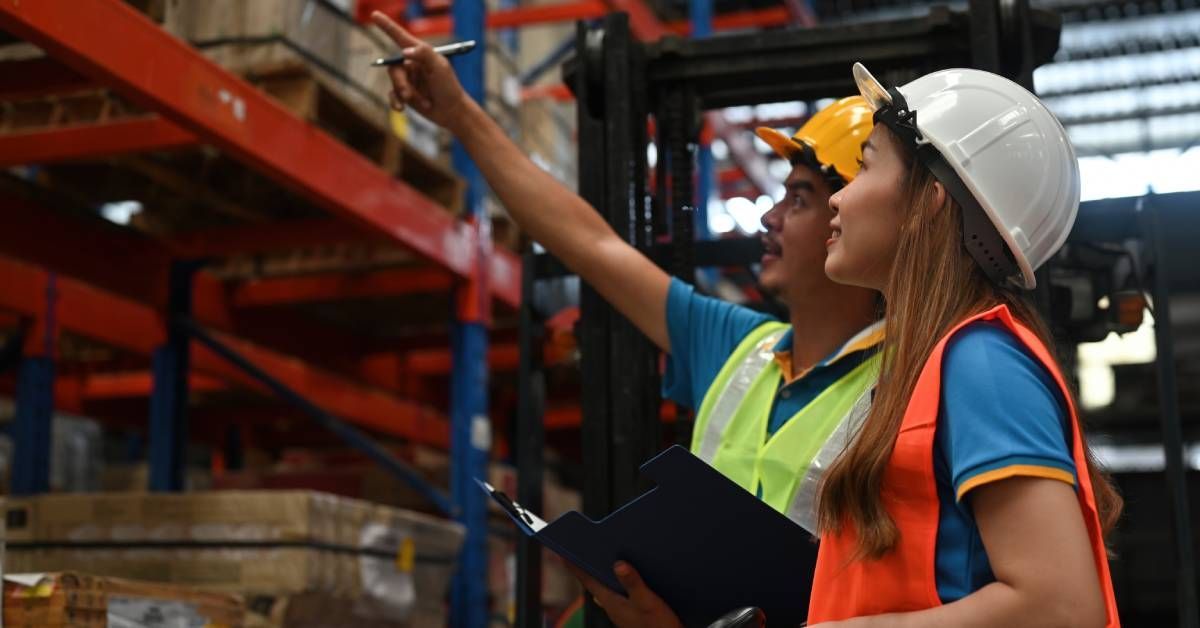
Risks You Might Find During a Rack Inspection
During a rack inspection, several common risks can come to light, each of which poses serious threats to your warehouse operations if left unaddressed.
Structural damage is among the most frequent issues, often caused by impacts from forklifts or general wear over time. Overloading is another prevalent problem, where racks are burdened with weights exceeding their designated capacity, leading to weakened structural integrity.
Additionally, improper installation or misaligned components can create hidden vulnerabilities in the system. These issues may not always be immediately visible, but they undermine the safety and functionality of your storage racks.
The consequences of these risks can be severe, extending beyond simple repairs. Structural issues can lead to rack collapses, creating hazardous conditions for employees and potentially causing serious injuries. Overloaded or improperly installed racks could result in damaged goods, leading to costly product losses and supply chain disruptions.
From a financial standpoint, delays caused by these problems can impact productivity and erode profitability. Addressing these risks promptly through regular inspections is not just about compliance but securing your workforce, protecting your inventory, and keeping your operation running smoothly.
Mitigating Potential Risks
Maintenance
Mitigating the risks identified during rack inspections requires a proactive approach and a commitment to safety. One key strategy is implementing a regular maintenance schedule to address structural issues or damage as soon as they are spotted. Maintenance could involve repairing damaged beams, replacing missing safety clips, or reinforcing weak areas to restore the integrity of your storage system.
Proactive Training
Staff training is another critical component. By educating your team on proper loading techniques and the importance of not exceeding weight limits, you can drastically reduce the likelihood of overloading-related incidents. Additionally, strictly adhering to manufacturer-recommended load capacities and maintaining proper installation practices ensures that your racks remain stable and reliable over time.
The benefits of these mitigation strategies extend far beyond compliance. By prioritizing safety, you can create a secure working environment, reducing the risk of employee injuries and safeguarding your inventory.
Improved safety also translates into fewer operational disruptions, as structurally sound racks are less likely to fail unexpectedly. This, in turn, enhances overall efficiency and helps maintain steady productivity.
Further, proactive risk management can lead to cost savings by preventing expensive repairs, product losses, and downtime. Over time, these measures contribute to a more resilient warehouse operation, showcasing the value of foresight and diligence in ensuring long-term success.
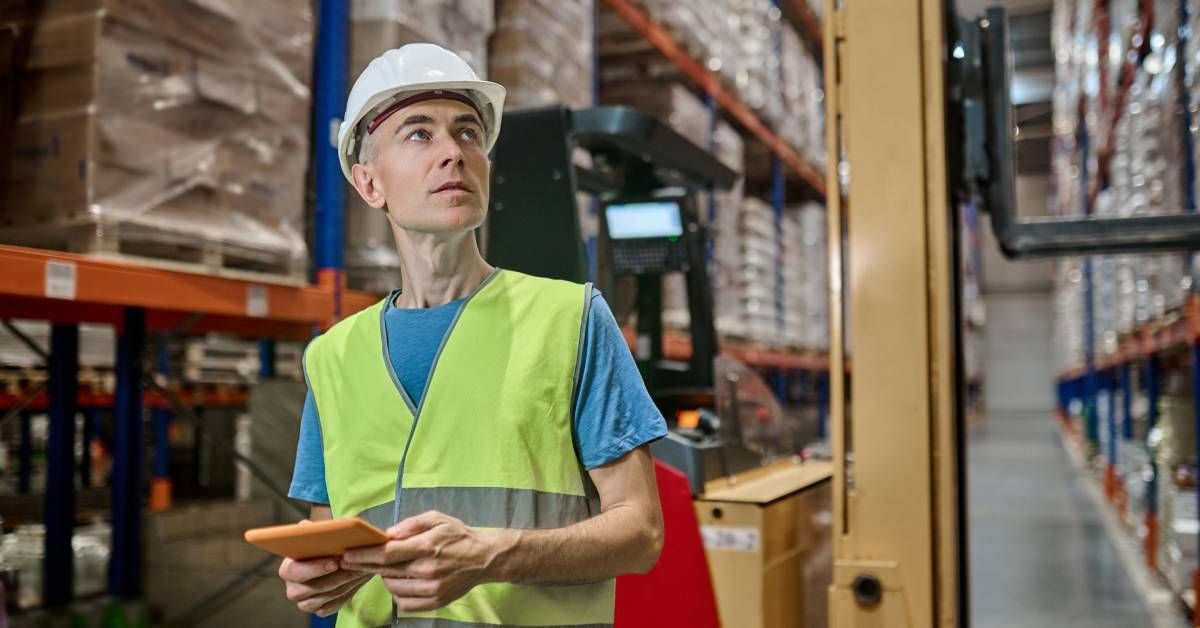
Other Tips for Optimizing Warehouse Storage
Maximizing warehouse storage efficiency involves implementing practical strategies that go beyond just organizing shelves.
Using vertical space is a game changer. Installing taller racks or multilevel shelving boosts storage capacity without expanding your warehouse’s footprint. An efficient inventory management system is equally crucial; you can stock and retrieve stock with minimal effort, reducing wasted time and resources.
Organizing products based on demand frequency, such as placing high-turnover items in easily accessible locations, speeds up order fulfillment and reduces labor costs. Regular audits of your storage practices can uncover inefficiencies and help you refine your layout for better flow and functionality. Additionally, integrating technology like automated storage systems or inventory-tracking software offers real-time insights and streamlines operations.
Beyond these strategies, fostering a culture of continuous improvement within your warehouse team can lead to innovative solutions and increased efficiency. Encourage staff to provide feedback on current storage practices and suggest improvements, as they often have firsthand insights into daily operations.
Moreover, collaborating with industry experts or consultants can offer fresh perspectives and advanced solutions tailored to your specific needs. By staying adaptable and open to new ideas, your warehouse can remain competitive and responsive to changing demands.
How Tyler Supply Company Can Help
Understanding how rack inspections can help identify and mitigate risks is vital for running smooth warehouse operations. When it comes to optimizing your warehouse storage and addressing potential risks, Tyler Supply Company is here to help. With a wide range of top-quality warehouse storage equipment and material-handling solutions, we bring expertise and dedication to support your business’s unique needs.
Our team understands the challenges of maintaining a safe and efficient warehouse, and we’re committed to providing tailored solutions that enhance your operations. Whether strengthening safety measures, improving efficiency, or upgrading your storage systems, Tyler Supply Company offers the tools and guidance to make it happen.