How To Simplify Inventory Tracking and Accuracy
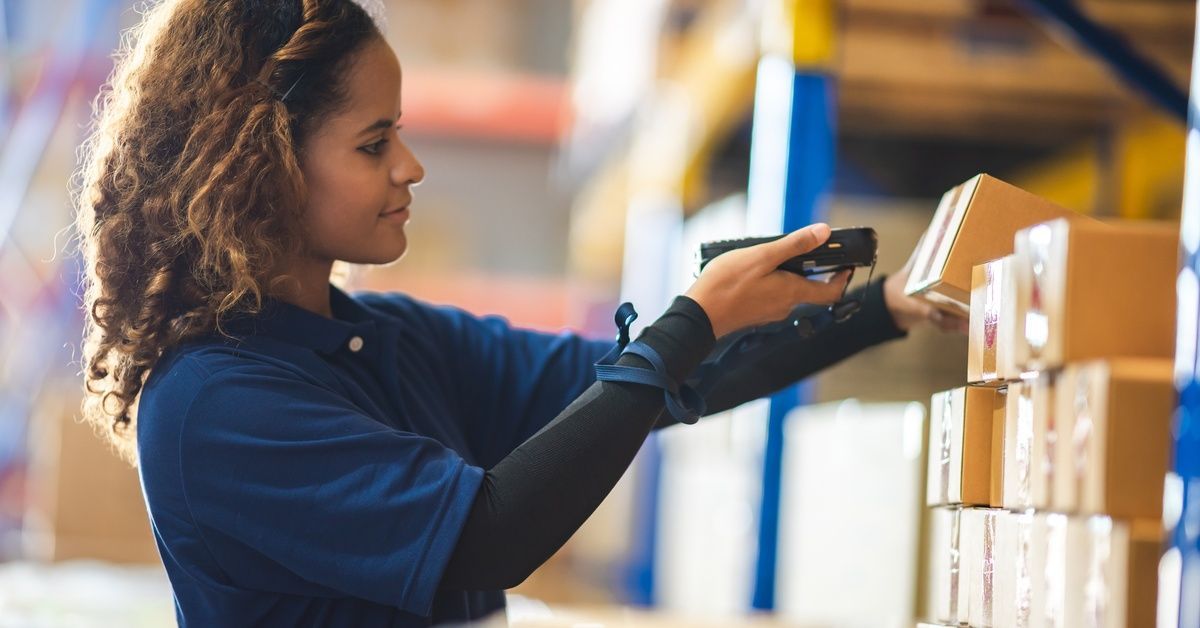
Managing inventory can often feel like juggling too many tasks at once. A misplaced product here, a forgotten restock there—these might seem small but can add up to significant losses. Businesses, from small shops to large enterprises, need reliable systems to keep things running smoothly. When inventory tracking is simplified and accurate, time is saved, money is conserved, and customer satisfaction soars. Thankfully, a mix of smart strategies and the right technology can transform the way inventory is handled. Read on to learn how to simplify inventory tracking and accuracy for your operations.
Why Optimizing Inventory Processes Matters
Optimizing inventory processes is essential for keeping businesses agile and efficient. When inventory is managed effectively, it minimizes errors such as overstocking or stockouts, which can lead to unnecessary costs or lost sales. By implementing streamlined processes, businesses can enhance their operations, reduce waste, and make better use of their resources. Accurate tracking ensures that stock levels reflect real-time data, which is invaluable when making purchasing or production decisions. It also improves communication across teams, creating a smoother workflow from procurement to delivery. Ultimately, optimized inventory management saves time and money while fostering a more productive and less stressful work environment.
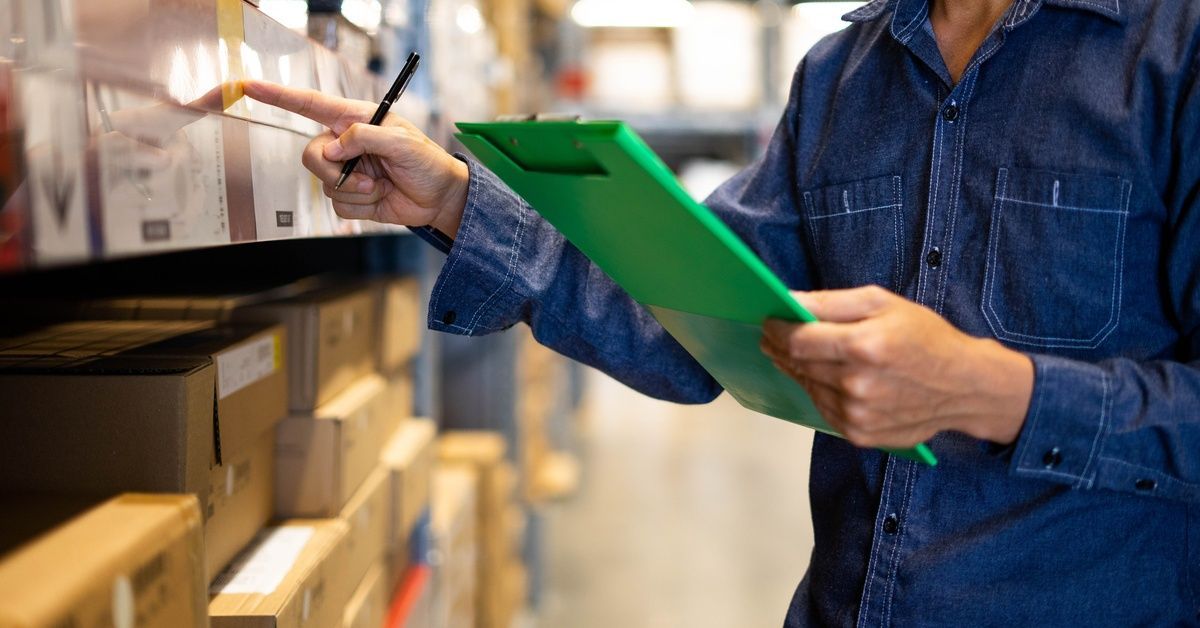
Beyond operational efficiency, proper inventory tracking has a direct impact on customer satisfaction. When stock levels are accurate, businesses can fulfill orders promptly, avoiding the disappointment of delays or unavailable products. Reliable inventory systems also enable proactive communication with customers, such as providing accurate delivery estimates or offering suitable alternatives during shortages. This instills trust and builds loyalty, giving businesses a competitive edge. Additionally, optimized processes make scaling operations easier as the company grows, ensuring consistency and reliability at every stage. The ripple effect of well-managed inventory extends beyond the warehouse, benefitting both the bottom line and the quality of customer relationships.
Tips for Simplifying Inventory Tracking and Accuracy
Simplifying inventory tracking doesn’t have to be complicated. By applying a few practical strategies, you can transform how your business manages inventory and reduce the risk of costly errors.
Standardize Your Processes
Consistency is key when it comes to effective inventory management. Standardized processes mean that everyone on your team is on the same page, reducing the chances of errors or miscommunication. Start by labeling all items with clear barcodes or QR codes, making them easy to track. Create uniform workflows for receiving, stocking, and fulfilling items so that each step is executed the same way every time. Training your staff on these standardized procedures guarantees they are equipped to follow them correctly, reducing inconsistencies.
Leverage Automation and Inventory Management Tools
The right technology can make a world of difference in inventory tracking. Automation through inventory management tools eliminates repetitive manual tasks, saving both time and effort. For instance, using cloud-based systems like Fishbowl or Shopify allows you to manage stock levels, track movements, and receive updates in real time. Additionally, barcode and QR scanners simplify data entry by ensuring instant and error-free identification of products. Integrating inventory tools with your sales platforms helps you avoid overselling or running out of stock. With these systems in place, you’ll enjoy improved accuracy, better insights, and the freedom to focus on growing your business.
Conduct Regular Audits
Inventory audits are an essential part of maintaining accuracy and catching small mistakes before they escalate. Conducting regular cycle counts, where small portions of your inventory are checked frequently, is far more manageable than occasional full-scale audits. This keeps your records up-to-date without disrupting daily operations. Scheduling counts during quieter periods ensures minimal impact on productivity and allows you to focus fully on the task. During the audit, verify how well your processes are being followed and spot any patterns of discrepancies. Regular audits not only improve accuracy but also build confidence in your tracking system.
Track Data Analytics for Continuous Improvements
Data is a powerful tool for optimizing inventory management. By consistently monitoring key metrics like stock turnover rates, reorder points, and shrinkage percentages, you can identify patterns and areas that need improvement. For example, tracking turnover can reveal whether a product is overstocked or underperforming, while shrinkage rates can signal issues like theft or mismanagement. Analyzing this data allows you to adjust purchase orders, streamline stock levels, and avoid bottlenecks. Many inventory tools come with built-in analytics features, making it easier to generate and interpret reports. Leveraging these insights ensures your processes constantly evolve, positioning your business to operate more efficiently and profitably.
Implementing Your Improved Processes
Introducing new inventory processes can come with hurdles, especially during the initial transition phase. Resistance from team members is a common challenge, as employees may feel uneasy about learning new methods or using unfamiliar tools. This can lead to errors or slower workflows as teams adapt to the changes. To overcome this, focus on clear communication and effective training. Explain why the changes are necessary, emphasizing how they will make tasks easier and more efficient in the long run. Offering hands-on sessions and ongoing support will help staff become comfortable with the new processes and confident in their abilities.
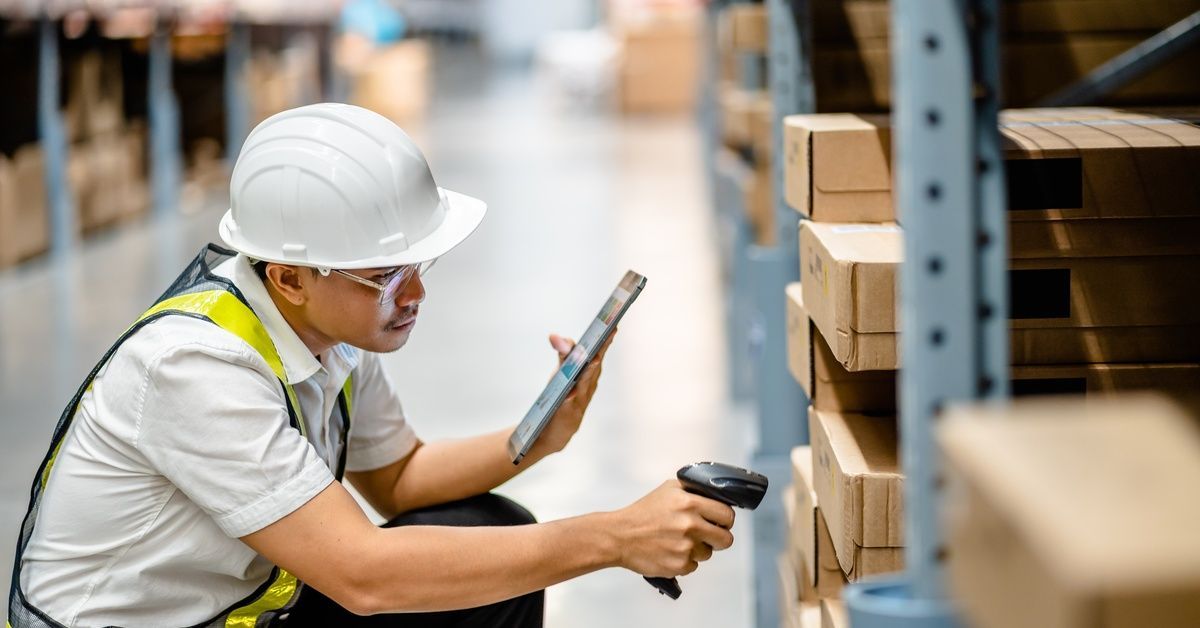
Another common obstacle is the cost and time investment required to implement improved systems. Businesses may hesitate to upgrade tools or adopt new software, worrying about expenses and potential disruptions to operations. However, these investments often pay off in the form of long-term savings and improved productivity. To mitigate concerns, start with scalable solutions that align with your budget and offer gradual implementation options. For example, you can begin by automating specific high-impact areas, like order tracking, before expanding to other functions. Regularly tracking progress and celebrating wins along the way not only ensures sustainable integration but also builds trust in the processes among all stakeholders.
How Tyler Supply Can Help
Simplifying inventory tracking and improving accuracy are vital steps toward building a more efficient, cost-effective, and customer-focused business. By leveraging strategies like standardizing processes, utilizing automation tools, and tracking insightful analytics, companies can revolutionize the way they manage stock. Implementing these changes not only saves time and reduces errors but also streamlines operations, benefitting both your team and your customers. While the path to optimized inventory processes may come with challenges, the rewards far outweigh the hurdles. With reliable systems in place, businesses can respond faster to market demands and scale operations confidently.
At Tyler Supply, we understand the complexities of inventory management and are here to make your transition seamless. Our comprehensive handling and storage solutions are designed to support businesses at every stage, whether you’re organizing materials in a small workspace or managing a large supply chain. Explore our range of durable, efficient equipment, from shelving systems and pallets to modular storage units customized to your needs. With Tyler Supply, you’ll find solutions to simplify your workflows and maximize space, helping you maintain greater inventory accuracy.