Optimizing Pallet Rack Layouts for Maximum Storage
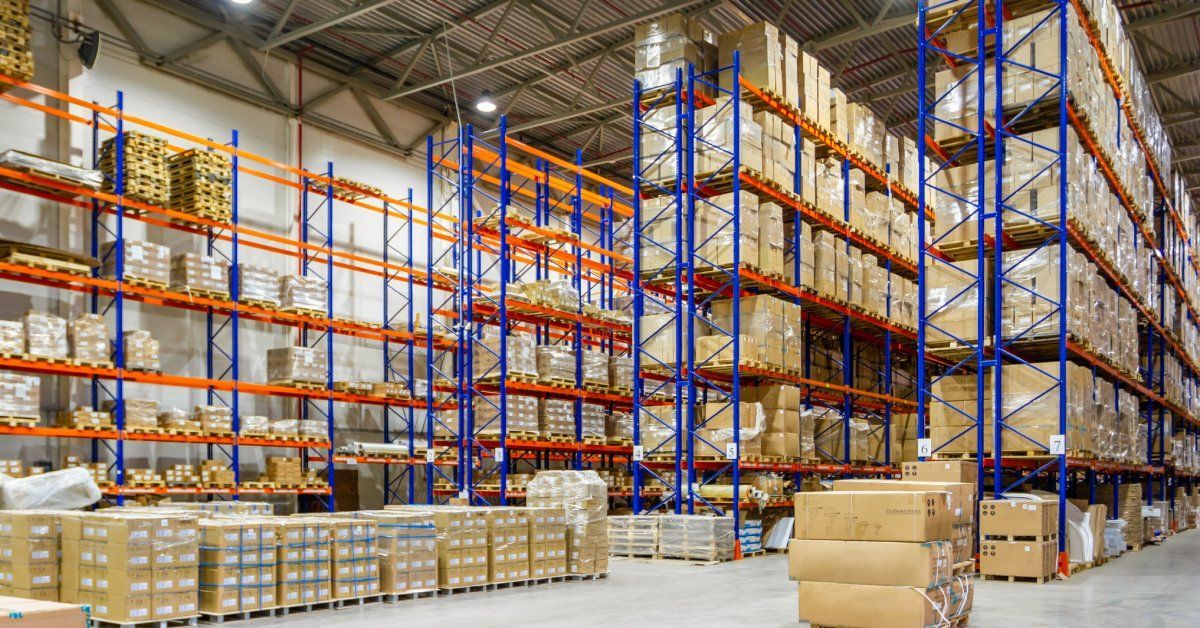
Efficient storage is at the heart of every successful warehouse operation. With growing demands for space and speed, maximizing your storage capacity has never been more important. A well-organized pallet rack layout can transform how your warehouse functions, elevating efficiency and safety. But how do you make the most of your available space without overcomplicating things?
Whether you’re starting fresh or revamping an existing setup, understanding the core principles of upgrading your pallet racks can simplify the process. Read on to learn everything you need to know about optimizing pallet rack layouts for maximum storage capacity.
Characteristics of an Optimized Pallet Rack Layout
There are three main pillars of an optimized pallet rack layout: efficient use of space, accessibility, and safety. We’ll explore each in detail below.
Efficient Use of Space
Efficient use of space is the foundation of an optimized pallet rack layout. By taking full advantage of vertical and horizontal space in your warehouse, you can significantly increase storage capacity without expanding your floor area.
For example, implementing taller racks or double-deep configurations allows you to store more pallets in the same footprint. Strategic layout decisions, like minimizing unused gaps between racks or pallets, reduce wasted space and enhance density. Additionally, grouping similar inventory ensures better organization while saving time during retrieval. When space is maximized effectively, your warehouse can handle higher volumes of stock without sacrificing efficiency.

Accessibility
Accessibility is equally important in achieving an optimized pallet rack layout. Employees need clear, unhindered access to stored items to maintain smooth operations. Properly sized aisles that align with equipment such as forklifts or reach trucks ensure safe and efficient navigation.
Accessibility also involves strategic placement of high-demand or fast-moving items, making them quicker to pick and reducing downtime. Utilizing well-labeled racks and zoning systems further simplifies locating inventory, boosting accuracy and productivity. An accessible layout doesn’t just improve speed; it also minimizes congestion and confusion, creating a more organized workflow.
Safety
Safety is the third pillar of an optimized pallet rack layout, ensuring employee well-being and protecting inventory. Overloading racks, for instance, can lead to dangerous collapses, so adhering to proper weight limits is essential. Clear aisle pathways also reduce the risk of accidents, allowing workers and machinery to move smoothly and safely. In addition, incorporating safety features like guardrails, pallet stops, and anti-collapse mesh mitigates injury risks.
Regular inspections and maintenance of your racks can identify damage or wear before they become bigger issues. You should also train employees on proper loading techniques and rack usage to ensure everyone understands how to operate within the limits of the system. A safe layout provides peace of mind, allowing operations to continue without unnecessary hazards.
Maximizing Your Storage Capabilities
Now that you understand what makes an optimized layout, follow these steps to maximize your storage capabilities.
1. Conduct a Space Audit
The first step in maximizing your storage capabilities is conducting a thorough space audit. This involves analyzing your current warehouse layout and identifying underutilized areas or inefficiencies.
Measure your vertical and horizontal space, noting areas where racks could be extended or reconfigured. Tools like 3D modeling software or warehouse management systems can provide insights into how your storage is being used.
By understanding your inventory flow and storage needs, you can determine if adjustments such as narrower aisles or taller racks are feasible. A space audit sets the foundation for making deliberate changes that enhance capacity and functionality.
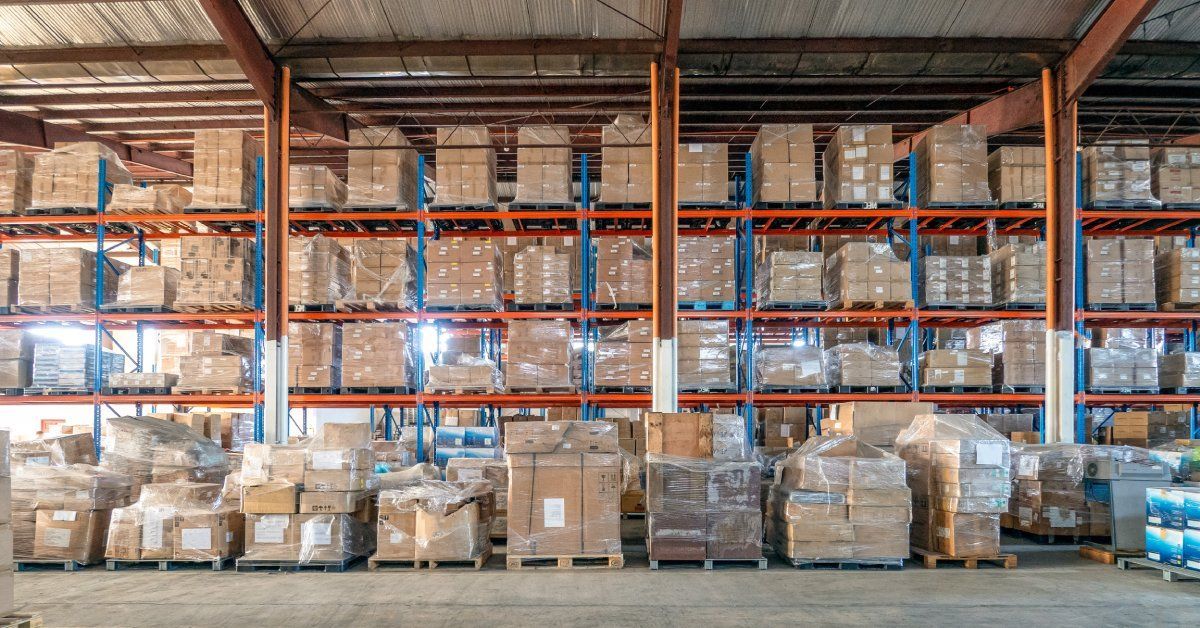
2. Implement Zones
Implementing effective zoning strategies is another effective way to improve storage efficiency. Divide your warehouse into distinct zones based on inventory characteristics such as size, weight, or demand levels.
Fast-moving items should be placed closer to packing or shipping areas to reduce retrieval times, while bulky or slow-moving goods can be stored in less accessible areas. You can also create zones for items requiring specific conditions, like temperature-controlled environments, to streamline processes further.
Proper labeling and signage within these zones help workers locate inventory quickly and accurately. A well-organized zoning system also prevents overcrowding in high-traffic areas, enhancing efficiency and safety.
3. Leverage Technology
Leveraging technology and automation takes storage optimization to the next level. Warehouse management systems (WMS) can help you monitor inventory levels, track item locations, and even suggest layout improvements based on real-time data.
Automation solutions, such as automated storage and retrieval systems (ASRS), maximize vertical space by enabling high-density storage. These systems also speed up picking and replenishment tasks, reducing labor costs and increasing throughput.
Barcode scanning and RFID tracking further streamline inventory management, helping you stay organized and accurate. By incorporating technology, you not only make better use of your space but also future-proof your warehouse against growing demands.
Common Mistakes To Avoid
You know what to do to organize your warehouse’s layout; now let’s discuss what not to do.
Neglecting Safety Standards
One of the most common mistakes in pallet rack layout design is neglecting safety standards. Overloading racks beyond their weight limits can lead to dangerous collapses, potentially causing injuries and damage to inventory. Skipping regular inspections for wear and tear is another oversight, increasing the risks of structural failures over time. A lack of attention to proper aisle spacing can also create hazardous conditions, as tight pathways hinder equipment movement and increase the chances of accidents.
To avoid these issues, adhere to recommended weight limits, invest in regular maintenance, and ensure aisle designs accommodate your equipment safely. Prioritizing safety is not just a regulatory requirement but a critical factor for achieving long-term operational efficiency.
Poor Planning
Another frequent pitfall is poor planning during the layout design phase. Many warehouses miss the opportunity to maximize vertical space by underestimating the value of taller racks or adjustable shelving systems. Improper inventory placement can disrupt workflows, as frequently accessed items may end up stored in hard-to-reach locations.
Additionally, failing to consider scalability can leave warehouses unequipped to handle future growth, leading to wasted resources and inefficient expansions. Overloading racks with mismatched pallets or ignoring inventory categorization further complicates operations, reducing productivity.
To counter these mistakes, focus on forward-thinking designs, logical inventory zoning, and scalable solutions tailored to both current and future business needs. Careful planning ensures your layout remains functional and adaptable.
How Tyler Supply Can Help!
Optimizing pallet rack layouts is key to creating a warehouse with maximum storage capacity. By addressing factors like space utilization, accessibility, and safety, businesses can enhance their storage capabilities and reduce operational challenges.
Whether you’re addressing common pitfalls or implementing advanced technologies, the benefits of streamlining your pallet rack layout are undeniable. A well-designed system will maximize storage, improve workflow, and ensure the safety of employees and inventory alike. Taking the time to analyze your current setup and make strategic adjustments will lead to long-term cost savings and improved productivity.
At Tyler Supply, we specialize in helping businesses like yours achieve superior results with top-tier industrial pallet racks and storage solutions. Our extensive product range includes customizable racking systems designed to adapt to your specific needs. With years of experience and a commitment to quality, our team offers expert advice to help you create layouts that are efficient, scalable, and safe.
Whether you’re overhauling your entire system or making targeted upgrades, we provide the tools and support needed to transform your warehouse operations. Explore our storage solutions today, and see how Tyler Supply can be your trusted partner in maximizing your storage potential.